SPALARNIE ŚMIECI
Metody termicznego przekształcania odpadów - Spalarnie odpadów
Jednym z głównych elementów instalacji termicznego przekształcania odpadów czyli (spalarni śmieci) jest kocioł lub piec obrotowy, których dobór oraz konstrukcja zależą od przyjętej metody spalania. Możemy spotkać się z następującymi technologiami spalania:
- Spalanie w nadmiarze tlenu.
- Piroliza oraz zgazowanie.
Spalanie w nadmiarze tlenu:
Jest to najstarsza znana metoda termicznej wykorzystywana przez spalarnie odpadów. Wywodzi się ona ze spalania paliw konwencjonalnych takich jak węgiel. Metoda ta polega na dozowaniu powietrza do spalania w takich ilościach, aby współczynnik nadmiaru powietrza był λ>1. Z doświadczeń ENERGO-SPAW wynika, że w przypadku spalania paliw alternatywnych, ze względu na niejednorodność oraz niższą zawartość węgla organicznego sugeruje się prowadzenie procesu tak, aby stężenie tlenu w spalinach wynosiło ok. 7%. Niższa wartość współczynnika nadmiaru powietrza może powodować niedopalenie się odpadów.
Zaletą prowadzenia procesu termicznego przekształcania odpadów przy nadmiarze powietrza przez spalanie odpadów, jest jego prostota. Nie bez znaczenia jest również łatwiejsza konstrukcja kotłów i pieców obrotowych, co decyduje o niższych kosztach inwestycyjnych.
Wadą prowadzenia procesu termicznego przekształcania w nadmiarze tlenu przez spalarnie śmieci jest zwiększona emisja zanieczyszczeń do środowiska, w tym wzrost stężenia NOx w spalinach. Dużą niedogodnością jest również zwiększona szybkość korozji elementów stalowych spowodowana wysoką zawartością w spalinach kwaśnych gazów takich jak SO2, HCl, HF wraz z występowaniem tlenu.
Rozwinięciem technologii termicznego przekształcania odpadów w atmosferze utleniającej jest tak zwana metoda reburningu.
Reburning polega na ponownym dodaniu do spalin paliwa reburningowego, które ma na celu obniżenie współczynnika nadmiaru powietrza w strefie spalin do λ <1, co prowadzi do powstania atmosfery redukcyjnej. Niedobór tlenu powoduje wystąpienie procesu redukcji niektórych związków chemicznych, w tym NOx.
Reakcje zachodzące w strefie reburningu (inaczej w strefie redukcyjnej):

Następnie spaliny wraz z paliwem reburningowym są dopalane w atmosferze utleniającej przy nie- wielkim nadmiarze powietrza. Jako paliwo reburningowe najczęściej stosuje się gaz ziemny, ale można zastosować również inne palne gazy lub paliwa ciekłe, które odparują w temperaturze prowadzonego procesu. Aby proces reburningu przyniósł spodziewane efekty, niezbędne jest bardzo dobre wymieszanie spalin z paliwem reburningowym. W związku z tym nie należy stosować paliw stałych w charakterze paliwa reburningowego.
Reakcje zachodzące w strefie dopalania:
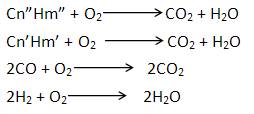
Wadą stosowania metody reburningu jest konieczność użycia dodatkowego paliwa, co sprawia, że spalarnie odpadów odnotowują zwiększone koszty eksploatacji instalacji.
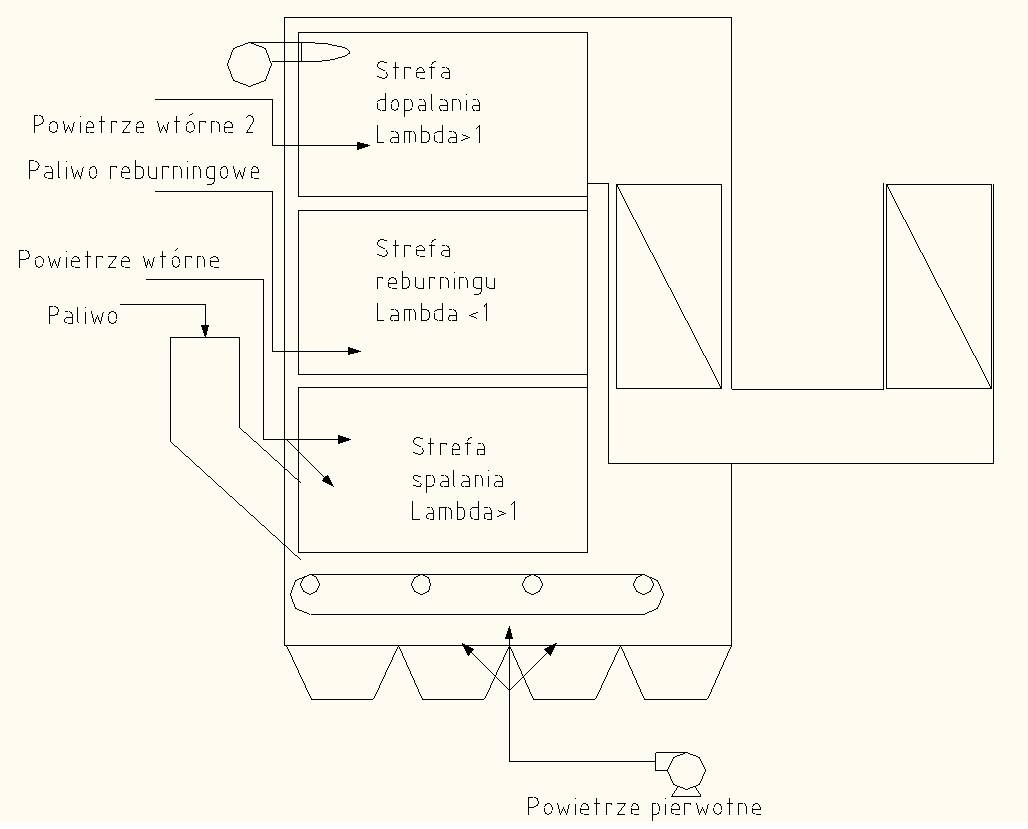
Rys 2. Schemat kotła z technologią reburningu
Piroliza oraz zgazowanie
Piroliza jest to proces redukcji związków organicznych na prostsze związki w wyniku działania wysokiej temperatury bez dostępu tlenu. W wyniku prowadzenia procesu pirolizy powstają gazy pirolityczne składające się głównie z CO
2, CO oraz CH
4 i frakcje ciekłe, w skład których wchodzą oleje, kwasy organiczne, proste alkohole oraz woda. W wyniku prowadzenia procesu pirolizy powstaje również frakcja stała czyli tak zwany karbonizat składający się głównie z węgla, metali i substancji mineralnych. Przybliżony skład gazu pirolitycznego w zależności od temperatury przedstawiono w tabeli 2 [3].
Tabela2. Skład gazu pirolitycznego w zależności od temperatury procesu [3]
Składnik gazu pirolitycznego [%] |
Temperatura procesu pirolizy [oC] |
482 |
648 |
815 |
926 |
H2 |
5,56 |
16,58 |
28,55 |
32,48 |
CH4 |
12,43 |
15,91 |
13,73 |
10,45 |
C2H4 |
0,45 |
2,18 |
2,24 |
2,43 |
C2H6 |
3,03 |
3,06 |
0,77 |
1,07 |
CO |
33,5 |
30,49 |
34,12 |
35,25 |
CO2 |
44,77 |
31,78 |
20,59 |
18,31 |
Wartość opałowa gazów pirolitycznych wynosi średnio 12-16MJ/Nm
3.
Drugą metodą termicznego przekształcania odpadów w atmosferze redukcyjnej jest zgazowanie. Proces zgazowania polega na termicznym rozkładzie związków organicznych przy niewielkiej ilości tlenu. W praktyce proces zgazowania realizują spalarnie śmieci poprzez spalanie odpadów przy niedoborze tlenu. Powietrze pierwotne jest dozowane w ilościach niezbędnych do utrzymania temperatury w piecu na poziomie ok. 600
oC. W opisanej sytuacji dochodzi do niecałkowitego spalenia związków węgla. Głównymi składnikami gazu powstałego podczas zgazowania paliw stałych jest CO
2, CO, CH
4, H
2 oraz woda. Średnia wartość opałowa gazu uzyskanego podczas procesu zgazowania wynosi od 5 do 10MJ/Nm
3[3].
Zarówno gaz pirolityczny jak i gaz uzyskany podczas zgazowania wymaga dalszego dopalenia. Proces dopalania prowadzi się przy współczynniku nadmiaru powietrza λ>1. Gazy pirolityczne i pochodzące ze zgazowania można po oczyszczeniu i odwodnieniu wykorzystać również jako paliwo do silników spalinowych napędzających generator energii elektrycznej. Jednak w przypadku gazów uzyskanych z przekształcania odpadów wykorzystanie ich do napędu silników jest mocno ograniczone ze względu na silnie właściwości korozyjne.
Kolejnym problemem związanym ze stosowaniem technologii zgazowania lub pirolizy przez spalarnie odpadów jest zagospodarowanie frakcji stałej czyli tak zwanego karbonizatu. Znaczna zawartość węgla oraz wartość opałowa na poziomie 20MJ/kg uniemożliwia składowanie karbonizatu na wysypiskach. Nie ma możliwości poddania karbonizatu procesowi pirolizy lub zgazowania. Jedynym sensownym sposobem utylizacji jest jego termiczne przekształcenie przy nadmiarze powietrza, ale wiąże się to z emisją zanieczyszczeń, czemu technologia zgazowania i pirolizy miała pierwotnie zapobiegać.
Nie bez znaczenia jest również skomplikowana budowa reaktorów do pirolizy, w które wyposażone są spalarnie śmieci. Charakter procesu wymaga utrzymania szczelności całej instalacji. Warto pamiętać również o wybuchowym charakterze gazów pirolitycznych, co wymusza stosowanie odpowiednich zabezpieczeń instalacji.
Urządzenia do termicznego przekształcania odpadów
- Kotły rusztowe
Spalarnie śmieci wykorzystują najczęściej najprostsze palenisko do termicznego przekształcania odpadów - ruszt. Kotły rusztowe są z powodzeniem stosowane od wielu lat w przemyśle energetycznym do spalania paliw stałych takich jak węgiel kamienny. Od spodu pod ruszt dostarczane jest powietrze pierwotne, a w komorze dopalania nad rusztem podawane jest powietrze wtórne. Cząsteczki popiołu w większości przelatują przez oczka rusztu do specjalnych lejów wypełnionych wodą, gdzie są gaszone.
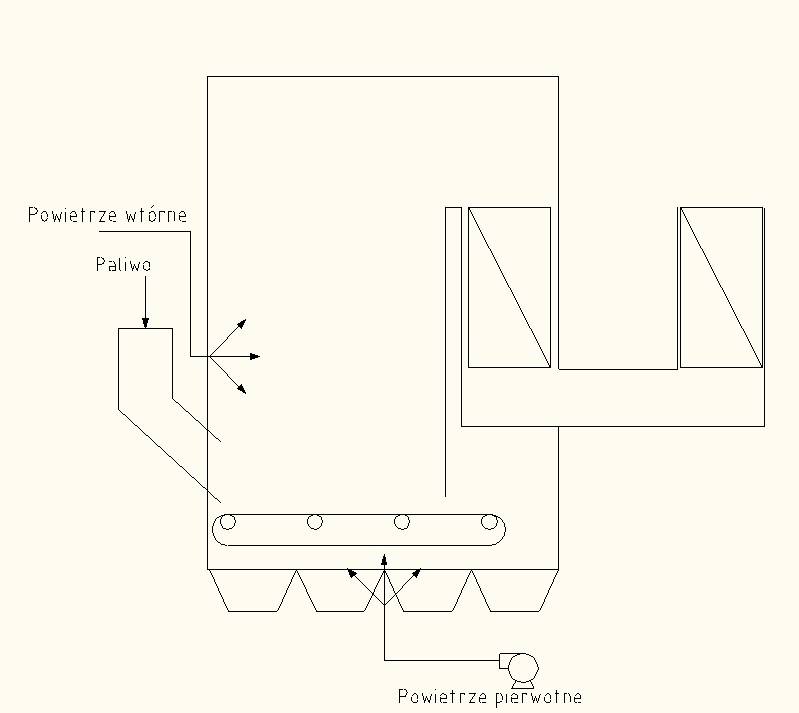
Rys 3. Schemat kotła rusztowego
W Nowoczesnych spalarniach odpadów, w których zachodzi proces termicznego przekształcania odpadów, kotły z rusztem ruchomym prostym nie sprawdzają się. Słaby proces mieszania się paliwa alternatywnego z powietrzem powoduje, że w otrzymanym popiele znajduje się duża część niedopalonego paliwa alternatywnego. Dużym problemem przy zastosowaniu kotła rusztowego może okazać się również żywotność rusztowin. W przypadku termicznego przekształcania paliwa alternatywnego typu RDF może następować przyśpieszone zużycie rusztowin na skutek intensywnej korozji wywołanej dużą zawartością chloru. Na skutek nierównomiernego napowietrzenia złoża oraz nierównomiernego rozkładu temperatury na ruszcie dochodzi również do zwiększonej emisji NOx. W kotłach rusztowych w przypadku spalania mączki mięsno-kostnej lub karbonizatu z procesu pirolizy, następuje porywanie cząsteczek paliwa alternatywnego. Cząsteczki paliwa opuszczają palenisko w stanie niedopalonym, co czyni kotły rusztowe bezużytecznymi, w przypadku termicznego przekształcania wymienionych odpadów.
Rozwinięciem koncepcji kotła z rusztem ruchomym płaskim, jest kocioł z rusztem ruchomym schodkowym. Zastosowane rozwiązanie zapewnia lepsze wymieszanie się paliwa z powietrzem, jednak zwiększa ilość odpadów, które przelatują przez rusztowiny nie ulegając spaleniu.
Podobnie jak w przypadku kotła z rusztem ruchomym płaskim, kocioł z rusztem schodkowym nie nadaje się do termicznej utylizacji mączki mięsno-kostnej oraz karbonizatu z procesu zgazowania.
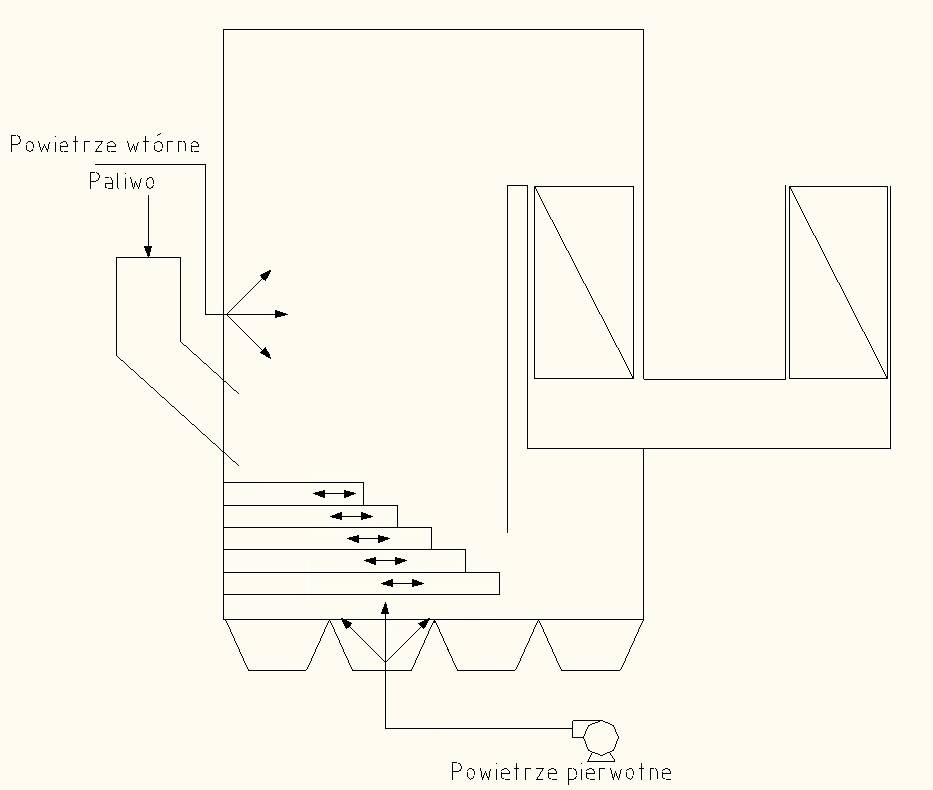
Rys 4. Schemat kotła z rusztem schodkowym.
W przypadku kotła z rusztem schodkowym jako wadę należy wymienić również konieczność okresowej wymiany rusztów, która wiąże się ze znacznymi kosztami. Z powyższym problemem często borykają się spalarnie odpadów.
- Kotły fluidalne
Proces fluidyzacji polega na wytworzeniu ruchomego złoża ciała stałego, pod wpływem przepływającego z odpowiednią prędkością, strumienia gazu. Schemat kotła fluidalnego przedstawiono na rysunku 5.
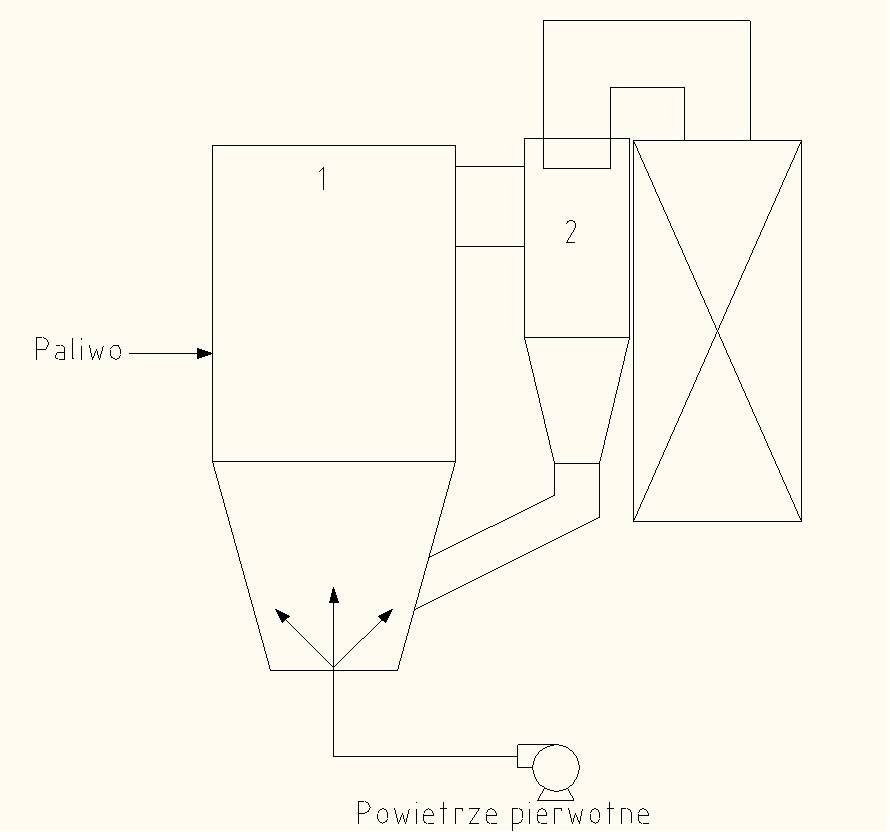
Rys 5. Schemat kotła fluidalnego. 1 kocioł fluidalny, 2 zintegrowany cyklon.
W kotle fluidalnym powietrze podawane pod ruszt unosi cząstki paliwa wytwarzając złoże fluidalne. Główną zaletą przedstawionego procesu jest bardzo dobre natlenienie złoża paliwa oraz znaczne rozwinięcie powierzchni kontaktu cząstek paliwa z powietrzem. Dodatkowo dzięki burzliwemu przepływowi mieszaniny paliwa i powietrza uzyskuje się bardzo równomierny rozkład temperatur w kotle. Proces spalania fluidalnego prowadzi się tak, aby temperatura złoża nie przekroczyła wartości T=900oC. Spalanie przy wyższej temperaturze może spowodować mięknienie popiołu i jego zbrylanie, co prowadzi do powstawania cięższych cząstek, które nie mogą utrzymać się w złożu fluidalnym. Spalarnie śmieci, które stosują kotły fluidalne wykorzystujące stosunkowo niską temperaturę wystarczająca w przypadku termicznego przekształcania paliw alternatywnych takich jak RDF, jednak jest niewystarczająca do spalania odpadów medycznych lub odpadów niebezpiecznych. W przypadku spalania mączki mięsno--kostnej, ze względu na drobny charakter cząstek istnieje obawa, że cząstki paliwa alternatywnego mogą zostać wywiane i nie ulegną całkowitemu spaleniu.
Kotły fluidalne można stosować zarówno do spalania w atmosferze utleniającej jak i do procesu zgazowania. W przypadku procesu zgazowania, atmosferę ubogą w tlen uzyskuje się przez częściowe zawracanie strumienia spalin do komory spalania kotła fluidalnego.
W przypadku spalania w złożu fluidalnym warto zwrócić uwagę na niewielkie możliwości regulacji mocy kotła – jest to problem z którym często spotykają się spalarnie odpadów. Jeżeli zmniejszymy moc poniżej określonej wartości i jednocześnie ograniczymy ilość powietrza zużywanego do spalania, istnieje ryzyko, że nie wytworzy się złoże fluidalne. Spalarnie śmieci muszą również odpowiednio rozdrobnić paliwa. Zbyt duże fragmenty podawane do termicznego przekształcenia mogą być za ciężkie i nie wytworzą złoża fluidalnego, a zbyt drobne paliwo może zostać wywiane z komory spalania i w konsekwencji nie ulegnie całkowitemu spaleniu.
- Piec obrotowy
Bardzo ciekawą alternatywną dla przedstawionych kotłów rusztowych oraz fluidalnych wykorzystywanych przez spalarnie śmieci, jest piec obrotowy - kocioł z przedpaleniskiem obrotowym. Płaszcz pieca obrotowego jest zbudowany z poziomej rury, pochylonej pod niewielkim kątem w stronę wylotu, której średnica oraz długość jest dostosowana do ilości spalanego paliwa. Płaszcz pieca obrotowego jest wprawiony w ruch obrotowy względem osi rury. Ruch płaszcza powoduje przesypywanie się złoża paliwa wewnątrz pieca dzięki czemu paliwo ulega ciągłemu mieszaniu i natlenieniu. Dzięki pochyleniu pieca obrotowego oraz wprowadzeniu go w ruch następuje powolny transport palącego się paliwa, żużlu oraz popiołów w kierunku wyjścia z pieca. Przednia część pieca jest zamknięta nieruchomą głowicą, w której jest umieszczony wlot paliwa, wlot powietrza, oraz palnik rozpałkowy. Piece obrotowe wykonane z betonów żarowytrzymałych znalazły szerokie zastosowanie w cementowniach do wypalania klinkieru. Wysoka odporność termiczna oraz chemiczna wymurówek ceramicznych pozwoliły na zastosowanie pieców obrotowych zarówno w procesach spalania paliw alternatywnych jak i odpadów niebezpiecznych i medycznych – spalarnie odpadów wykorzystują je powszechnie. Piece obrotowe sprawują się bardzo dobrze przy termicznym przekształcaniu paliw alternatywnych typu RDF jak i paliw sypkich takich jak karbonizat lub mączka mięsno-kostna.
Zastosowanie wymurówki ceramicznej ma jednak pewne wady. Duża masa ceramicznych pieców obrotowych podnosi wydatek energetyczny potrzebny do wprawienia i utrzymania pieca w ruchu. Dodać należy również, że wymurówki ceramiczne mogą ulegać kruszeniu oraz erozji pod wpływem zmiennych warunków termicznych, ściernego charakteru pyłów oraz czynników chemicznych. Regeneracja wymurówki jest procesem drogim i długotrwałym. Problemem może być również uszczelnienie połączenia głowicy przedniej z ruchomym płaszczem. Przez powstałe nieszczelności może być wciągane do wnętrza pieca fałszywe powietrze, co jest szczególnie niebezpieczne w przypadku prowadzenia procesu zgazowania.
Wychodząc naprzeciw problemom związanym z eksploatacją ceramicznych pieców obrotowych przedsiębiorstwo ENERGO-SPAW zaproponowało oraz przetestowało nową, innowacyjną konstrukcję pieca obrotowego, z którego mogą korzystać spalarnie odpadów. W rozwiązaniu ENERGO-SPAW zastosowanym w Prototypowej Instalacji Termicznego Przekształcania Odpadów użyto piec obrotowy własnej konstrukcji, w którym ciężki ceramiczny płaszcz został zastąpiony płaszczem stalowym. Schemat pieca obrotowego autorstwa ENERGO-SPAW przedstawiono na rysunku 6.
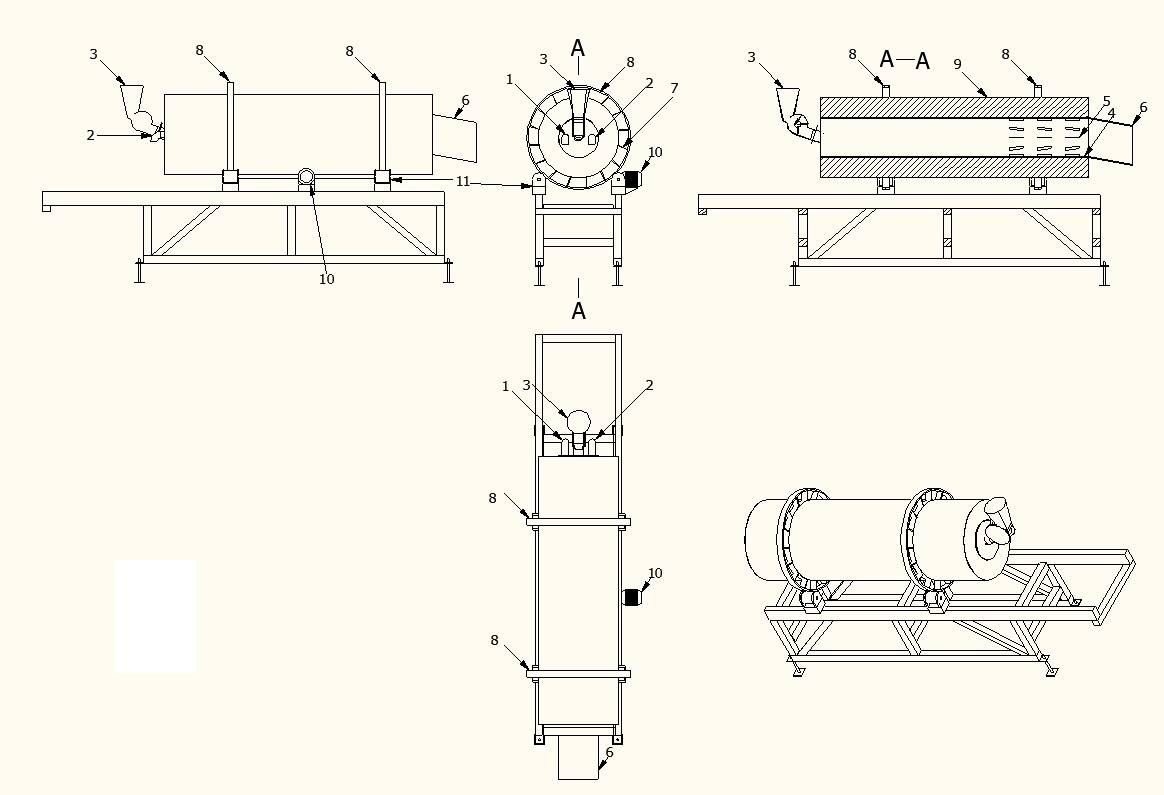
Rys 6. Piec obrotowy ENERGO-SPAW. 1 rura palnikowa, 2 kanał powietrza wtórnego, 3 wrzutnik paliwa, 4 stalowy płaszcz pieca, 5 przegrody zwalniające złoże paliwa, 6 kanał wylotowy pieca obrotowego, 7 szprychy mocujące obręcz toczną, 8 obręcz toczna, 9 izolacja termiczna, 10 silnik napędowy.
Zastosowanie specjalnej stali żarowytrzymałej pozwoliło na znaczne zmniejszenie masy pieca obrotowego oraz wyeliminowanie problemu eksploatacyjnego związanego z renowacją wymurówki ceramicznej. Zastosowanie odpowiedniego gatunku stali pozwala na prowadzenie procesu termicznego przekształcania odpadów w maksymalnej temperaturze 950oC, co jest wystarczające w przypadku spalania paliw alternatywnych typu RDF, mączki mięsno-kostnej czy karbonizatu. Konstrukcja pieca obrotowego ze stalowym płaszczem została tak przemyślana, że w przypadku zużycia płaszcza jego wymiana na nowy zajmuje wykwalifikowanej ekipie remontowej jeden dzień. Spalarnie śmieci zyskują zatem innowacyjne i niezawodne urządzenie. Testy przeprowadzone przez ENERGO-SPAW w ramach budowy oraz badań Prototypowej Instalacji Termicznego Przekształcania Odpadów potwierdziły przydatność pieca obrotowego z płaszczem stalowym w procesie termicznego przekształcania paliw alternatywnych takich jak RDF, mączka mięsno-kostna i karbonizat z procesu zgazowania słomy.
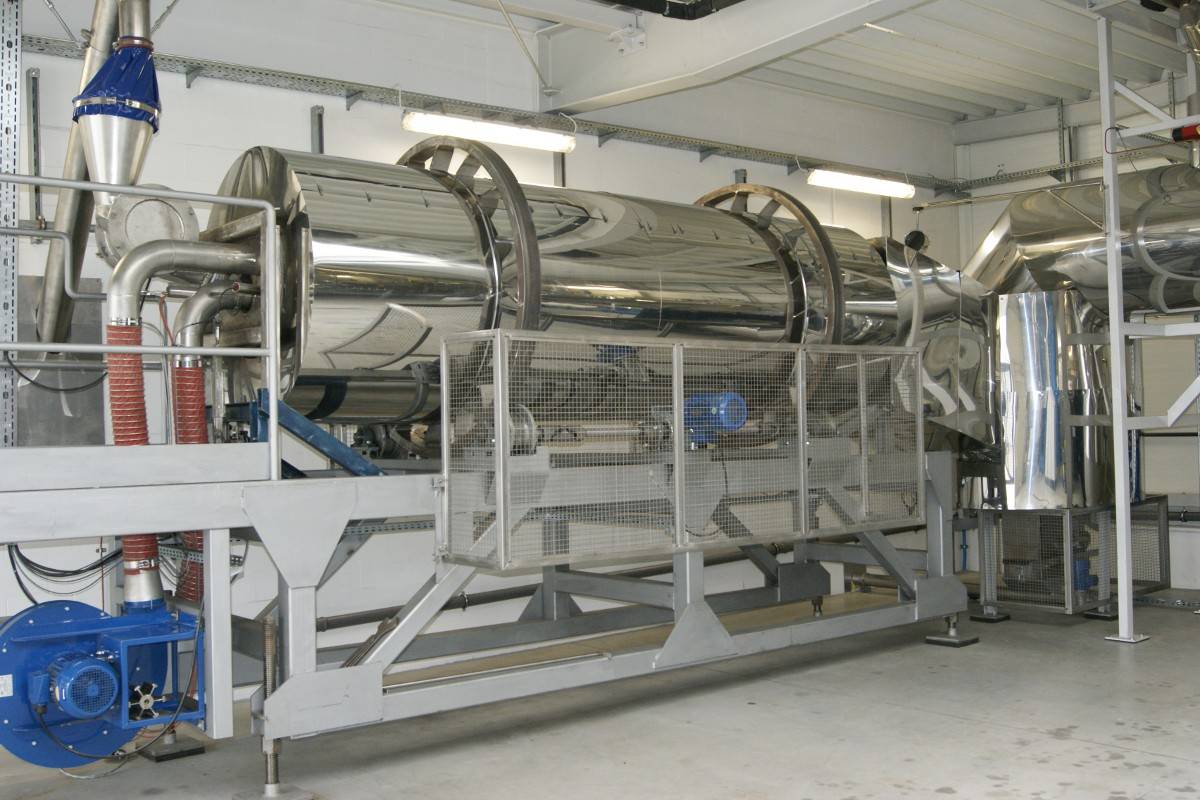
Rys 6. Piec obrotowy ENERGO-SPAW.
LITERATURA
- ,,Przegląd technologii termicznego przekształcania odpadów’’ dr hab. inż. Grzegorz Wielgosiński, Nowa Energia nr 1/2011.
- ,, Zastosowanie przemysłowe technologii reburningu” , mgr inż. Krzysztof Majewski, Piece przemysłowe & kotły, IX/X 2013.
- ,,Określenie potencjału odpadów i ich rodzajów do produkcji stałych paliw alternatywnych” Prof. dr hab. inż. Jerzy Walendziewski, dr inż. Marek Kułażyński, inż. Andrzej Surma,
Sieć Naukowo-Gospodarcza ,,Energia” Wrocław, styczeń 2007.
Opracował:
Krzysztof Pittner – inżynier projektant systemów termicznej utylizacji odpadów, odzysku ciepła i oczyszczania spalin.
ENERGO-SPAW, styczeń 2014 r.